CONTRIBUTORS | DATE CREATED | VERSION |
---|---|---|
Findhan Strain; Conor Newman | 18 July 2018 | V1.0 |
A Comparison of The Use of Convectional Heating and Infra-Red Heating in Out of Autoclave Curing of Carbon Fibre Composites
Summary
This paper describes the systematic investigation into the comparisons between a traditional convection oven and a novel infrared (IR) heating set-up when applied to the curing of an out of autoclave carbon fibre / epoxy laminate. Two aerospace grade carbon fibre panels were cured, one using IR heating and one with a convection oven. The IR cure profile adhered to the intended cure schedule much more accurately than the convection cure with good through-thickness temperature control, demonstrating that standard convection oven cure is not a fit and forget process as is typically believed. Specimens were water jet cut and evaluated using dynamic mechanical analysis and flexural testing to draw comparisons in physical properties. The glass transition temperature and flexural modulus of the convection cured sample was found to be higher (mean of 7.36°C and 3.72GPa respectively): it is proposed that this is because of an extended cure time of the convective method (additional 70 minutes) and potentially due to moisture variation in samples during testing. The flexural strength of the IR samples was 57MPa higher (mean) due to high porosity levels in the convection sample, again due to an extended period of low resin viscosity associated with the poor control in a convection oven. IR has thus demonstrated very good ability to accurately control the cure of carbon fibre composites.
Ceramicx would like to extend our thanks to Kemfast PASS and Cytec for providing material for this test.
Introduction
The need to move away from the widely documented drawbacks of the use of autoclaves for composite resin curing has seen an increased focus on out of autoclave (OOA) methods and materials, particularly within the aerospace sector in recent years. To date, the majority of OOA resin systems utilize some form of convection oven for curing and achieving the required material properties. The illusion of such an approach is that this is a ‘fit and forget’ technique where a desired ramp rate and cure temperature is programmed into the controller and the process completes.
Many engineers control from a lagging thermocouple, typically located underneath the part or a harder to heat area and this reading tends to be notably different from air temperature, temperatures on the material surface and temperatures located throughout the part thickness. While the eventual dwell temperature of this lagging thermocouple on the part can reach the intended cure temperature, the heating rate that the part has been exposed to tends to be significantly different from the programmed heating rate. These deviations can result in excessive/insufficient resin flow times leading to dry laminates) or excessive/insufficient time at the cure temperature. To combat this, cure schedules are often tweaked based on a part material / mass, tool material / mass and bagging arrangements and off-sets built into the system. While this is a perfectly acceptable means to achieve a good cure, it can take a developmental period to establish off-sets.
Infra-red (IR) curing has shown the ability to rapidly and accurately heat a wide range of materials, using the energy to directly heat a targeted part and limiting energy inefficiencies. Although IR curing will require some work initially to set-up the parameters of the process, it has been hypothesised that this is no different from accurate control of convectional curing, suggested above. This study therefore sought to compare the use of convection and IR in the curing of an OOA carbon fibre / epoxy laminate. Interestingly, it has long been suspected that IR curing also offers an enhanced ability to remove porosity from a laminate due to the vibrational nature of the energy transfer when it arrives at a material, however this is not part of the scope of this initial investigation. The scope of this study is to commence comparisons on the two methods of curing with a view to building initial data on the resultant material properties. It was understood from the outset that this would not be an exhaustive testing schedule.
Selecting Evaluation Criteria
A wide range of methods could potentially be used to evaluate the physical properties resulting from the two curing methods, however, as the primary function of heating is to initiate polymer cross- linking, it would be sensible to focus testing on resin dominated properties. Consequently, dynamic mechanical analysis (DMA) and flexural testing were chosen at the primary methods of physically testing the materials with a subsequent comparison of results to data logged during the cures. DMA testing provides a good understanding of the glass transition temperature (Tg) of polymers and a similar Tg would indicate a similar degree of cure. Flexural testing was chosen as a simple method of inducing tensile, compressive and shear forces into specimens and would give an indication as to the contribution of cure to multi-mode loading. The majority of matrix evaluation tests in composites are subjective to some extent and not fully quantifiable relative to the results of a test, therefore, similarity in method is the primary means by which a comparison can be drawn.
Method
The proposed testing route would give an indication as to the comparisons of IR curing vs Convective Curing and the resultant material properties. The method would only seek to provide a basic comparison and it was understood from the start that the analysis would not be comprehensive – merely a means by which an informed discussion could commence. The method undertaken was:
- Laminate two carbon fibre / epoxy panels
- Cure one panel using IR
- Cure one panel using Convection heat
- Water jet cut specimens
- Carry out dynamic mechanical analysis (DMA) testing
- Carry out flexural testing
- Analyse results
Laminate Preparation
Tooling
As the physical tests require flat specimens, a flat panel was manufactured using both methods and the same tool. A 12mm thick Invar plate was used for the testing aiming to replicate materials used within the aerospace industry. Figure 2.1 shows the invar tooling prior to laminating.
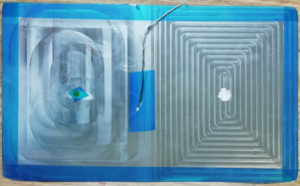
Material
This study sought to analyse the use of IR curing when compared to convective curing.
The objective of this study was to prove that IR curing can offer potential improvements in the processing of high value composites when compared with convective heating. Out of autoclave (OOA) pre-pregs were targeted as the application most likely to benefit from this.
A number of common OOA pre-pregs were short-listed as potential materials to be used for the test programme, as highlighted in Table 2.1 This table is not exhaustive but shows a sample of the higher temperature curing pre-pregs that are available for OOA applications.
Manufacturer | Product | Max Cure Temp °C |
---|---|---|
Tencate | E760 | 180 |
Tencate | E750 | 180 |
PRF | RP549 | 159 |
Gurit | SE200 | 195 |
Cytec | MTM 44-1 | 180 |
Multiple 120°C curing pre-preg systems are available for OOA applications however, the number of readily available pre-preg systems curing at 180°C is greatly reduced. Such pre-pregs tend to be reserved for aerospace applications and have consequential availability and minimum order quantities that mean many are unsuitable for small-scale testing. It was hypothesised that 180°C would be a more challenging temperature to attain uniformity of temperature through components than 120°C and thus, if good equalisation of temperatures can be proven at this value, then lower temperatures would be even more straight forward. (Indeed, 120°C curing has since been tested and proven to be extremely accurate using IR heating similar to the methods described in this report.)
Cytec MTM 44-1 was chosen as the pre-preg for this project due to its high-performance nature and typical aerospace applications. Furthermore, Cytec offered sample material to the project through Kemfast PASS and Ceramicx are grateful for this generosity. The pre-preg was supplied in twill weave at 285g/m2.
Lay-Up and De-bulking
Each ply for the proposed laminates were cut measuring 250mm x 130mm and placed on the tool.
2 plies were placed initially on the tool, followed by a 30 minute debulk. 5 further plies were placed followed by a 30 minute debulk. The remaining 7 plies were then placed down (flipped over to maintain a balanced laminate) and a final 30 minute debulk carried out before final bagging and curing.
Bagging Lay-out
The vacuum bagging sequence was defined to maximise efficiency of the IR cure. As IR is a direction- al energy, losses occur when any item is placed between the heat source and the targeted material. Therefore, losses occur due to vacuum bags, release films, peel plies, breather fabrics, etc and indeed this is true for any method of curing as such materials act as insulators to the targeted resin. Ceramicx have extensive data in the insulative effects of each material used in composites processing, including variances in manufacturer, product colour, temperature tolerance, etc. Consequently, it was decided that the lay-up would utilise edge breathing with only the release film and vacuum bag in place be- tween the heat source and the pre-preg. Conveniently, in this case, a non-perforated release film is also recommended by the pre-preg manufacturer but this is not always the case.
The laminate was sealed with sealant tape covered in release film acting as an edge-dam surrounding the pre-preg, as recommended by the pre-preg manufacturer. Peel-ply acting as the edge breathing medium overlapped the laminated by 5mm and was connected via breather fabric to the vacuum source.
Materials used were:
• Vacuum Bag – Vac Innovation VACleaseR1.2
• Non-perforated release film – Vac Innovation VACleaseR1.2 • Breather Fabric – Vac Innovation VACB4 polyester
• Peel-ply – Nylon
• Sealant tape – Vac Innovation VACsealY-40
The vacuum bagging lay-out was constructed as recommended in the pre-preg manufacturer’s technical data sheet, an extract of which can be seen in Figure 2.2. This was repeated for both methods to ensure consistency.
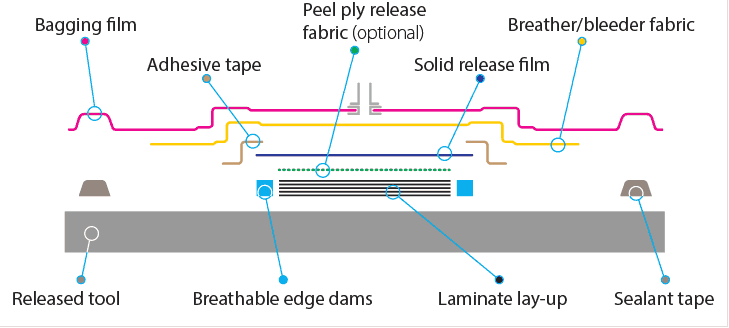
Cure Schedule
The targeted cure schedule for MTM 44-1 can be seen in Table 2.2. It can be seen that the recommended ramp rate is 1-2°C per minute. 1.5°C per minute was therefore chosen as a median value in this range.
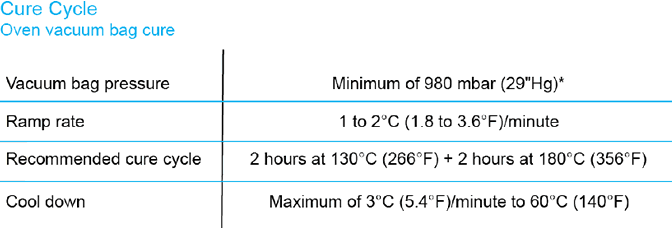
Curing Set-Up
The set-up used to cure the IR samples utilised a combination of hollow ceramic elements and quartz halogen tubes to ensure optimal temperature equalisation through the carbon fibre sample, as seen in Figure 2.3. The exact details of this curing schedule remain the intellectual property of Ceramicx and are therefore not disclosed; however, graphical outputs of temperatures recorded can be seen in Figure 3.1.
The convective sample was cured in a small convection oven at Ulster University and graphical outputs are displayed in Figure 3.2. (p7)
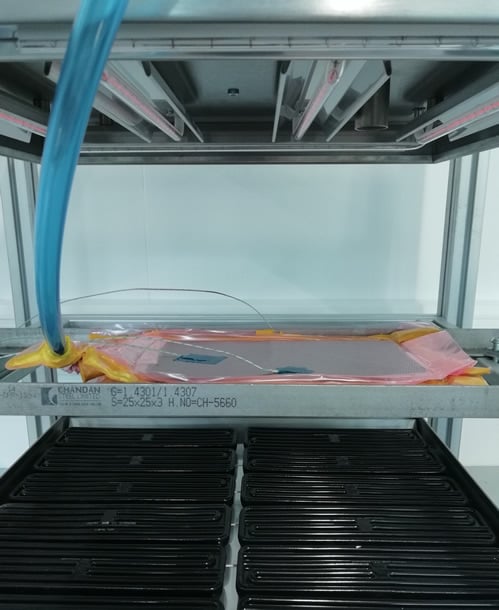
Results
The results obtained during the investigation are detailed within this section. Results are presented for the curing process in Section 3.1, dynamic mechanical analysis (DMA) in Section 3.2 and flexural testing in Section 3.3.
Curing
Figure 3.1 displays the cure profile associated with the IR panel and Figure 3.2 shows the recordings from the convection oven.
Figure 3.3 overlays the IR temperatures (Internal taken as an approximate average of both readings) with the convective temperatures. It can clearly be noted that there are large differences in readings in the convection sample due to the indirect application of heat compared to IR.
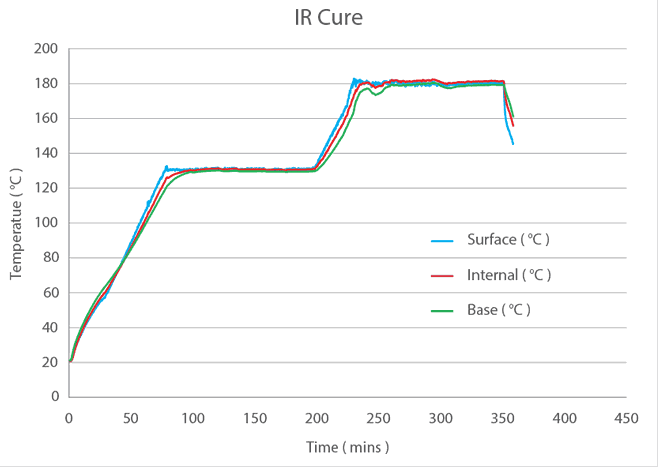
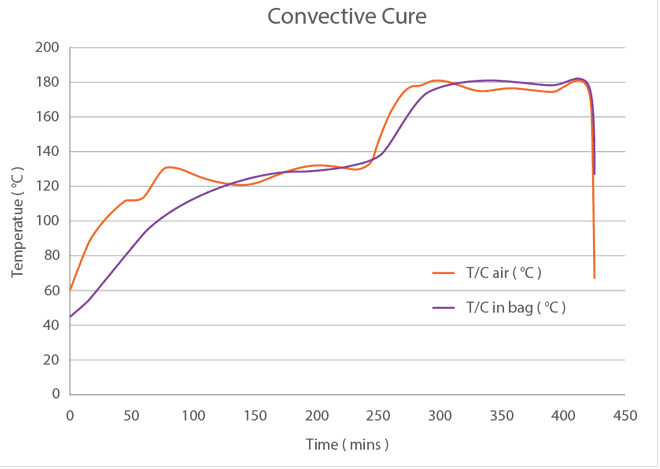
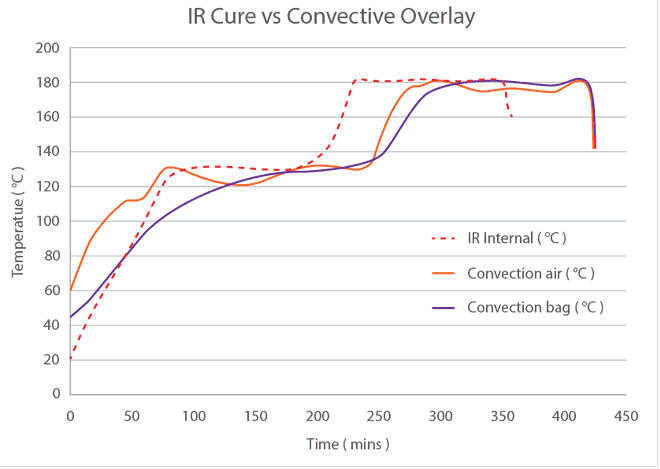
DMA Testing
Dynamic mechanical analysis (DMA) testing is used regularly to characterise the profile of polymers when subjected to heat and load.
The test was conducted in accordance with ASTM D7028-07 ‘Glass Transition Temperature (DMA Tg) of Polymer Matrix Composites by Dynamic Mechanical Analysis (DMA). The machine used was a TA Instruments Q800, as seen in Figure 3.4. Table 3.1 highlights the key test conditions undertaken on the TA Instruments Q800 DMA Machine.
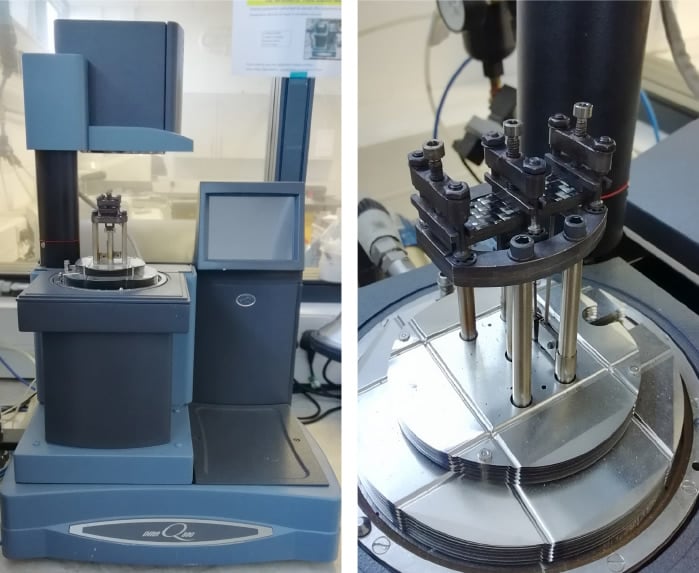
Machine | TA Instruments Q800 |
Mode | DMA multi frequency – Strain |
Test | Temp Ramp / Freq Sweep |
Clamp | Dual Cantilever |
Amplitude | 15 μm |
Soak Time | 5 min |
Final Temperature | 250 °C |
Ramp Rate | 5°C/min |
Frequency | Single |
Frequency | 1 Hz |
Figure 3.5 displays a graphical output of the typical DMA results where the Storage Modulus curve (E’) can be seen in green, the Loss Modulus in blue and Tan Delta in red. Table 3.2 then displays the numerical outputs from the analysis, with Tg figures quoted from Storage Modulus Onset and Tan Delta peak.
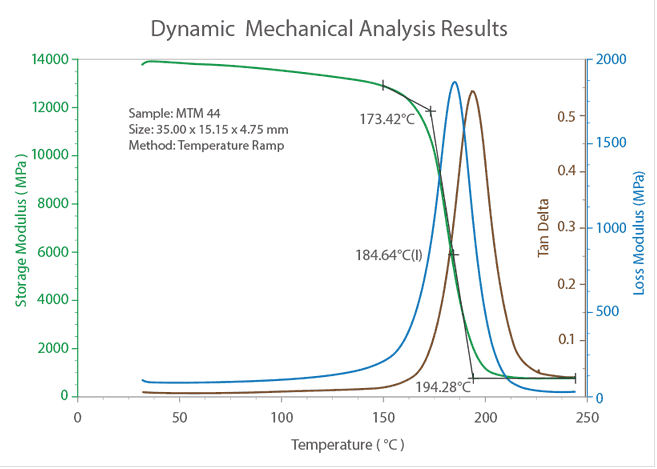
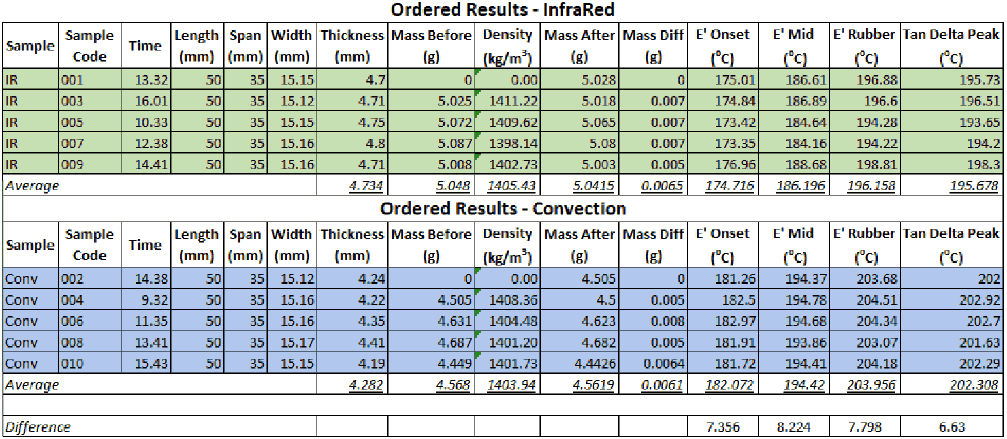
Flexural Testing
3 Point Bending (3PB) according to ASTM D7264 ‘Standard Test Method for Flexural Properties of Poly- mer Matrix Composite Materials’ was undertaken to identify key physical properties of the cured speci- mens. The testing was carried out at Ulster University using an Instron 5500R. An example of the set-up prior to testing can be seen in Figure 3.6.
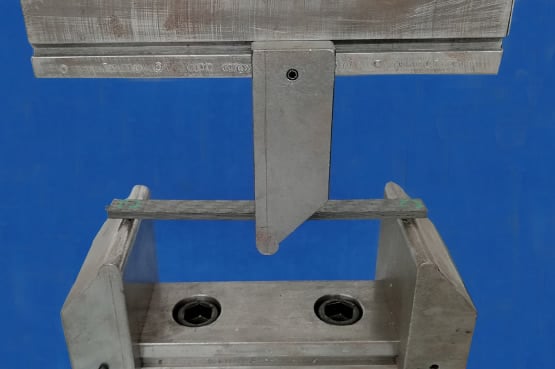
Data generated from 5 samples of Convective curried composites and 5 samples of IR cured composite was compiled into a Stress – Strain curve and can be seen in Figures 3.2 and 3.3 respectively. (p7)
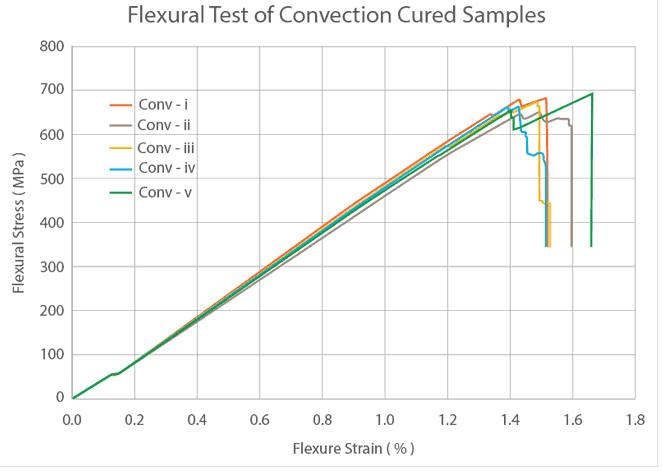
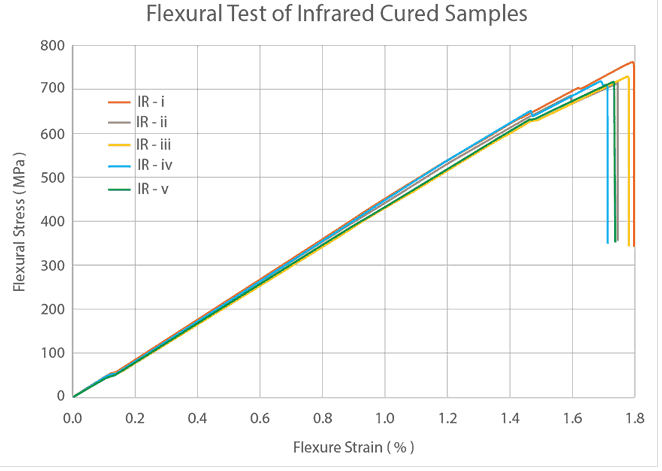
After analysis, the data was filtered to calculate the modulus from the straight-line portion of the Stress – Strain curve. The slope of the curve was extracted between 150MPa and 500MPa. Table 3.1 displays the Modulus and Flexural Stress for both methods.
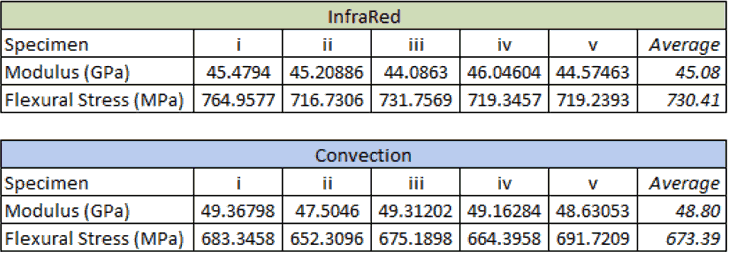
It is important to note that there were minor differences between the specimens that were likely to be the cause of these deviations and are discussed in greater detail in Section 4.0.
The broken specimens can be seen in Figure 3.9.
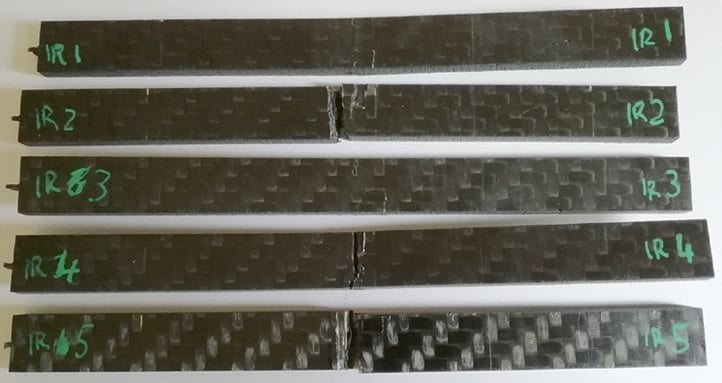
Discussion
Heat Profile Accuracy
From Figure 3.3, it can be seen that there were notable differences in the cure schedules that undoubtedly led to the differences in physical properties. For example, the convective sample remained in the oven 70 minutes longer than the IR sample and has obvious effects on not only total processing time but also properties such as fibre volume fraction (FVF) and Tg. Furthermore, on the convective sample, the thermocouple was placed within the bag at the side of the tool and potentially may have been insulated slightly by the breather, leading to higher temperatures being experienced (eg at 180°C) for slightly longer than the data indicates – again this could influence values such as Tg.
Convection as a Fit & Forget Method
Engineers tend to label convection ovens as a ‘fit and forget’ technology where any resin could effectively be cured. While this is true to some extent, it is very clear that the intended cure profile is not the same as the cure profile experienced by the part, as can be seen from Figure 3.3 The IR cure has shown very good accuracy in the control of temperatures underneath the laminate (ie on the tool), in the middle of the laminate and on the upper surface. Impressively, this was with a rapid set-up and certainly contributes to de-bunking the illusion that composite components can be cured easily in a convection oven.
Undoubtedly, the variances experienced within the convection oven could be narrowed and a more representative cure profile established but there would still be offsets to be programmed in and considerable lags when compared to IR curing. IR curing has a much faster response to these variances as it is a direct heating method, thus reducing overall processing time and energy used.
It is also important to note that significantly faster heat up rates could be achieved with IR than with convection and are limited in this study by the recommended rate for void removal by the pre- preg manufacturer. Ceramicx has data on heat-up rates for various aerospace tooling materials and are orders of magnitude greater than recommended rates for this resin system.
Exotherm
Control of exotherm is another potentially useful attribute to the use of IR in curing composites. When using pyrometers on the surface of the composite to control cure temperatures, the quartz halogen heaters can rapidly switch off or limit power in the event of resin exotherm increasing the cure temperature beyond the recommended cure schedule. This would be significantly faster than any reduction in temperature that could be achieved with a convection oven however the effect is unknown in this test.
Resin Content
Following curing of both panels, it could be clearly seen that too much resin was drawn from the sample cured in the convection oven, despite both laminates being de-bulked and bagged in the same manner, with solid release film and controlled edge breathing using peel-ply and breather. The resultant drier laminate from the convection oven is likely due to differing flow characteristics during the heat up phase of the cure. Although conversations with the pre-preg manufacturer have not been undertaken, it is likely that the flow of resin is critical during the heat up phase to 130°C prior to the 2-hour dwell at this temperature. The poor control of the convection oven hindered the ability to control resin in both laminates and hence the higher porosity levels seen in Figure 4.1
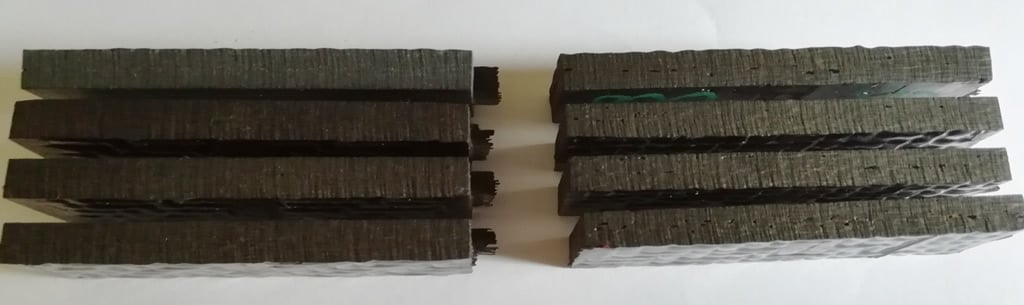
DMA and Glass Transition Temperature
Comparison of Tg in IR & Convection Samples
The average Tg attained with IR samples was 175°C and 182°C with convection samples. Although a lower Tg in this experiment could indicate an incomplete cure, it is highly unlikely given the measured temperatures within the IR lay-up. Therefore, it could be confidently stated that this difference is due to the extended oven cure time associated with the convective sample and the spiking temperatures within it. As noted in Section 4.1, the cure time for the convection sample was 70 minutes longer than the IR and it is known that Tg is influenced by cure temperature and time at that cure temperature, therefore the 7°C difference can clearly be accounted for. Furthermore, the short time between water-jet cutting and potentially inherent moisture levels could easily account for the variation in the samples. Typically, a 48-hour drying procedure would be used for specimens, but this was not undertaken for these samples, as described in 4.3.2.
Difference in Measured Tg and Datasheet Tg
The MTM 44-1 datasheet stipulates that Dry Tg at E’ Onset is 190°C and from discussions with Cytec, this particular batch was understood to be 194°C. Samples cured within this experimental report attained an average of 175°C (IR) and 182°C (Convection) which is still lower than the reference 190 °C. Nonetheless, this is not perceived to be an issue as it is known that many factors influence glass transition temperature within DMA testing. It is understood that Cytec reference SACMA SRM 18R-94 method for DMA analysis which is understood to suggest a heating rate of 5°C/min – the heating rate also used within this method. Therefore, primary differences may have arisen from the lack of conditioning of specimens. Samples were not conditioned as previously stated, as this is primarily a comparative study. Typically, this can take 48 hours in a hot, dry environment and it is widely known that moisture can lower the Tg of composites. A small difference in mass was observed in all samples following testing (approximately 0.12 – 0.15%) and it is unclear if this would have such a notable change from the stated datasheet value.
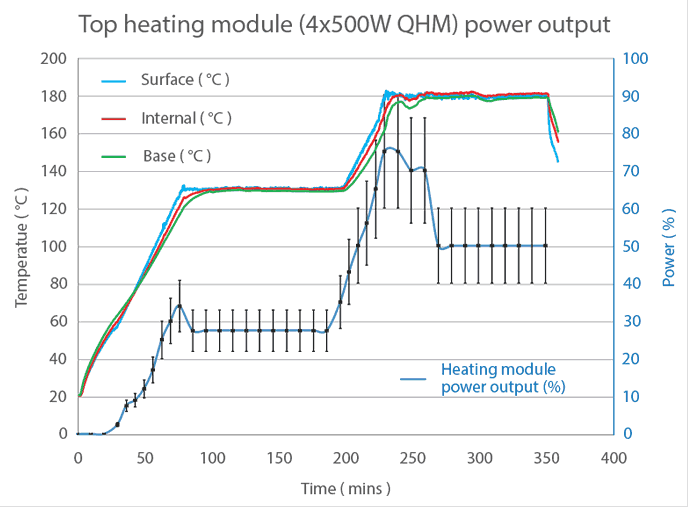
DMA Testing Discrepancies
Any notable omissions from the procedure required for ASTM D7028 should be noted and hence it is important to recognise a deviation from section 10, ‘Conditioning’ of samples. The recommended procedure is to condition for up to 48 hours, then seal samples in a moisture proof container. As the objective of this analysis was to provide comparative results instead of absolute results, this was not deemed necessary. The samples were water jet cut, hand dried and then allowed to dry in a hot sunny area for 3 hours. Samples were weighed before and after tests as recommended, then a sample from each batch was tested in an altering fashion so any effects of moisture from the surrounding environment would be shared in the results. A difference of 0.006g was noted before and after testing of samples but this variation was taken across a short time period as opposed to the 48 hours recommended conditioning.
Flexural Testing
From Table 3.1, it can be seen that there are differences in modulus and strength between both batches of samples. The modulus is higher in the convective samples by 3.8GPa on average. Although this has yet to be confirmed with the material supplier, it is likely due to the increased time at high temperatures as discussed in Section 4.3.
It is widely known that porosity levels can have a notable influence on the performance of composite materials, particularly those properties that are matrix / off-axis dominated such as flexural testing, (although the effects could potentially be limited by the woven material used). Therefore, higher porosity levels are likely to have contributed to the lower strength of the convective specimens with an average reduction of 57MPa.
Considering all of these aspects, the differences between the samples are likely to be minimal or nonexistent if an exact comparison was undertaken whereby component heating rates are identical.
Flexural Testing Discrepancies
There were small changes in the support span during the testing of both batches from a span : thickness ratio of 32 for the convective samples to 30.8 for the IR samples. This would translate to a small decrease in flexural strength for the IR samples however the effect is small and flexural strength for the IR samples would still remain notably higher. Indeed, the higher resin content of the IR specimens led to a greater number of resin ridges on the surface and thus a potentially greater measured thickness (with Vernier calipers) than that represented in the drier convection samples. As a result, this increased thickness could decrease the flexural strength and modulus slightly (as it is squared in the calculation of stress) and bring it very close to the convective samples.
Conclusions
The conclusions drawn from this study are:
- A comparison in material properties can be proven between IR and convection curing as small differences within this test can be accounted for:
- Although Tg and Flexural Modulus of the Convective samples is higher (mean of 7.36°C and 3.72GPa), this is likely due to an extended time at elevated temperature compared to the IR sample and potential moisture variations within the samples.
- Although Flexural Strength of the IR samples is higher (mean of 57MPa), this is likely due to a higher void level in comparative Convection samples.
- IR curing has demonstrated an ability to accurately control temperatures within an OOA aerospace grade carbon fibre laminate of approximately 4.5mm thickness.
- It has been shown that cure using a convection oven is not a fit and forget method with programmed heating rates not being representative of the heating rate that the part experiences. IR’s ability to respond rapidly to temperature variation ensures a greatly enhanced ability to match part temperature to intended temperature.
Disclaimer
This information is based upon technical data that Ceramicx believes to be reliable at this time. It is subject to revision as additional knowledge and experience are gained. Ceramicx holds no responsibility for the accuracy, completeness, or any third party’s use or the results of any information, apparatus, product, or process disclosed.