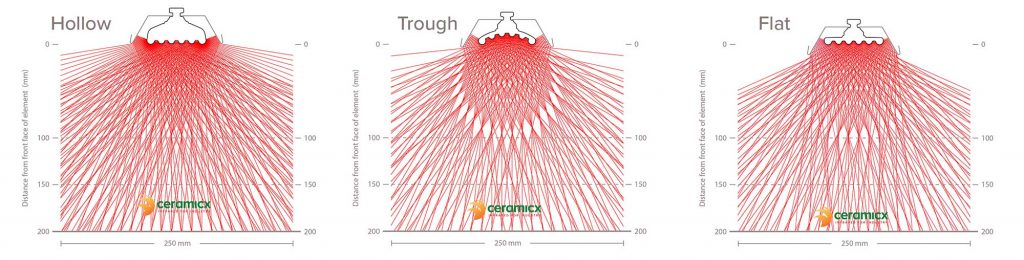
The use of infrared technology is continually advancing across many global commercial and industrial sectors. And, as a leading manufacturer of ceramic and quartz heating elements, our continued development means Ceramicx elements have transformed how infrared heat is used in a range of manufacturing applications.
But, with distinct differences between them, there can often be confusion about which element type is best to use for the
best results. So which Ceramicx infrared heating elements are best for your application?
What Ceramicx heating specialists need to know
To help you find the right element type for your requirements and system, the most important information for us to know is:
- The area you need to heat
- The power and type of element you need to use.
- The target material
This article should give you a head start making that choice.
Ceramic infrared heating elements | Hollow, Flat, or Trough?
A consistently popular radiant heat emitter range, industry-standard ceramic infrared elements are the most efficient element where long cycle times are required.
Ceramic Trough Elements – Long-wave trough elements produce a concentrated heat output that disperses over distance. Best suited to applications requiring emitters positioned further from the target material.
Ceramic Hollow Elements – Long-wave hollow elements filled with high-density insulating material, giving a significant reduction in rear heat loss with increased radiant output from the front of the element.
Ceramic Flat Elements – Long-wave flat elements produce higher operating temperatures and uniform heat output. Best suited to applications requiring emitters positioned closer to the target material.
Ceramic element fast facts
- Wattage: up to 1500W
- Temperature: up to 726°C
- Wavelength range: 3-10µm
- Heat-up time: ~10 minutes
- Most popular elements: FTE, FFEH, SFEH
Quartz infrared heating elements | Standard or Pillared?
Quartz infrared elements can be effective where rapid heater response and/or zone-controlled heat is needed.
Quartz Standard Elements – Short to medium-wave standard quartz heater elements consist of iron-chrome aluminium resistance wires inside highly reflective aluminium clad or stainless steel housing. Better suited to applications that involve continuous movement, their metal studs can withstand mechanical shock better than ceramic mounts of the pillared quartz element variation.
Quartz Pillared Elements – Short to medium-wave pillared quartz heater elements feature exactly the same technical and physical specifications but also include a pressed, ceramic pillar for mounting. With a 42 x 15mm punched slot in the reflector (max. thickness 1.5mm) and a supplied spring and clip, quartz pillared elements are designed for easy element replacement. The pillar also houses screw terminals for connection and can easily be interchanged for ceramic elements.
Quartz element fast facts:
- Wattage: up to 1000W
- Temperature: up to 772°C
- Wavelength range: 1.5-8µm
- Heat up time: ~5 minutes
- Most popular elements: FQE, PFQE
Quartz tube infrared heating elements | Halogen or Tungsten?
As a powerful heat emitter range, quartz infrared halogen and tungsten elements are used in fast-moving processes with shorter cycle times that require extremely high temperatures.
Quartz Halogen Elements – Short-wave quartz halogen heating elements use halogen gas to support the tungsten filament in reaching temperatures as high as 2600°C, with a peak wavelength emission of ~1.0µm.
Quartz Tungsten Elements – Medium-wave quartz tungsten heating elements use a porcupine or star type coil filament to reach operating temperatures up to 1500°C, with a peak wavelength emission of ~1.6µm.
Quartz Halogen and Tungsten element fast facts:
- Wattage: up to 2000W
- Temperature: up to 2600°C
- Wavelength range: 1-1.6µm
- Heat up time: instant
Ceramicx heating solutions
Infrared heat technology has the ability to deliver plenty of benefits to the user, whatever the process or application. Regardless of the demands, each ceramic, quartz, quartz halogen, or quartz tungsten infrared emitter provides precision heat where it’s needed, as well as being cost-effective and energy-efficient.
While delivering on cost and efficiency, making the right choice of Ceramicx infrared element will also mean:
- Reduced machinery or process downtime
- Reduced heat loss to machine surroundings
- Consistent process heating for a reduced product reject rate
- Less time and energy wasted replacing elements beyond essential maintenance
- Better results / better quality product
For more information, complete our enquiry form here or email at [email protected]. We’ll be happy to help you find the right heating solution for you and your business.
See also – Ceramicx FAQ page.